We perform contamination checks, damage assessments, and supplier compliance reviews on all incoming materials. Only defect-free materials enter production.
Quality Control
Beneco Packaging commits to providing the highest quality printing and continually strives for excellence by applying to the highest standard of certifications and environmentally ethical practices in the industry.
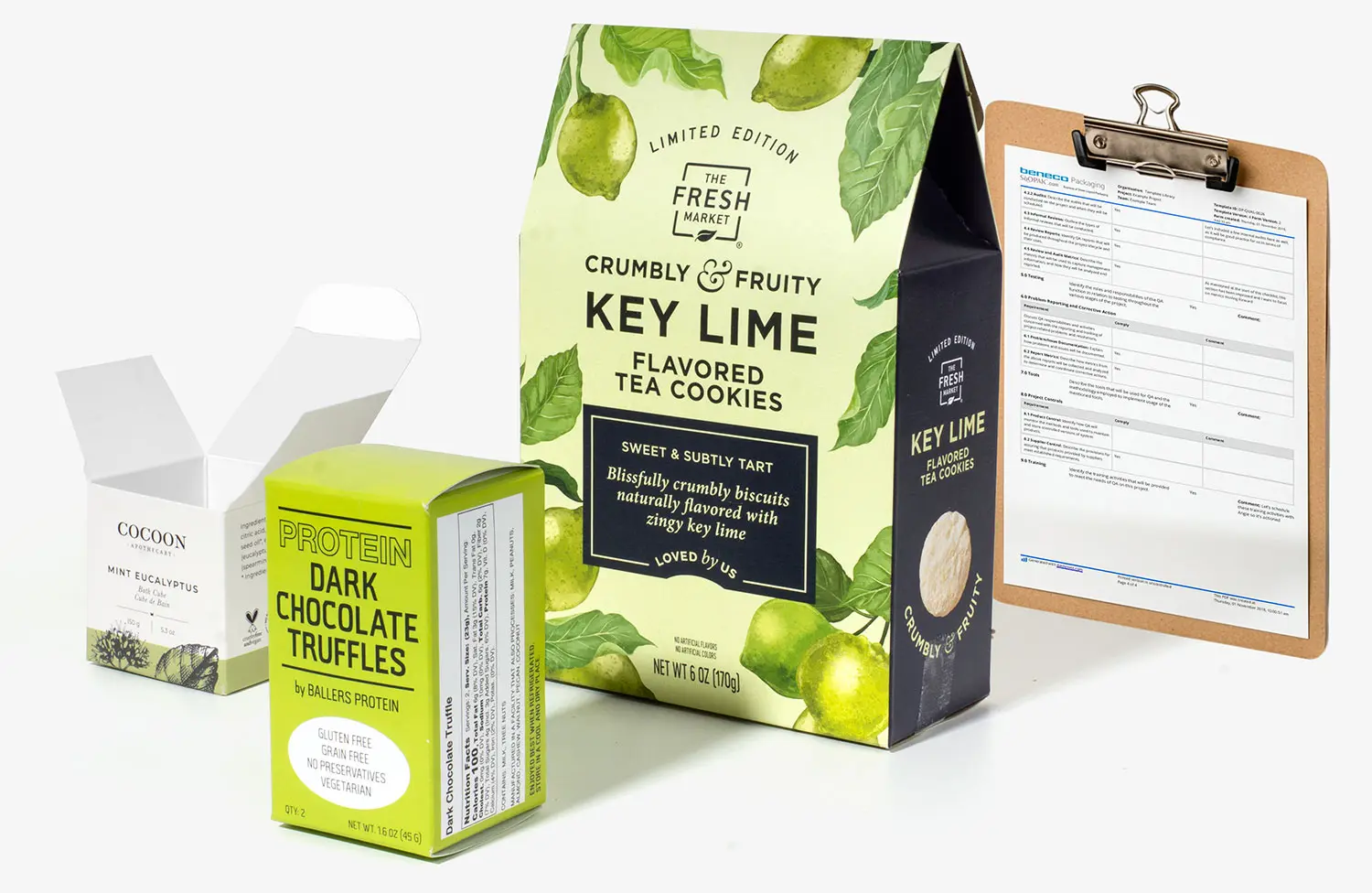
At Beneco Packaging, we are committed to delivering high-quality products that meet and exceed customer expectations. Our robust quality control (QC) process, along with our numerous certifications and awards, demonstrates our dedication to excellence. We ensure that every product we produce adheres to the highest standards.
How it work
Ensuring Excellence: Beneco Packaging’s Commitment to Quality Control
Incoming Materials Check
We inspect all raw materials upon delivery to ensure they’re undamaged and free of contaminants before use.
Production Checks
Quality checks are done at every stage (like printing, cutting, gluing) to catch issues early. Our QA team monitors the process continuously.
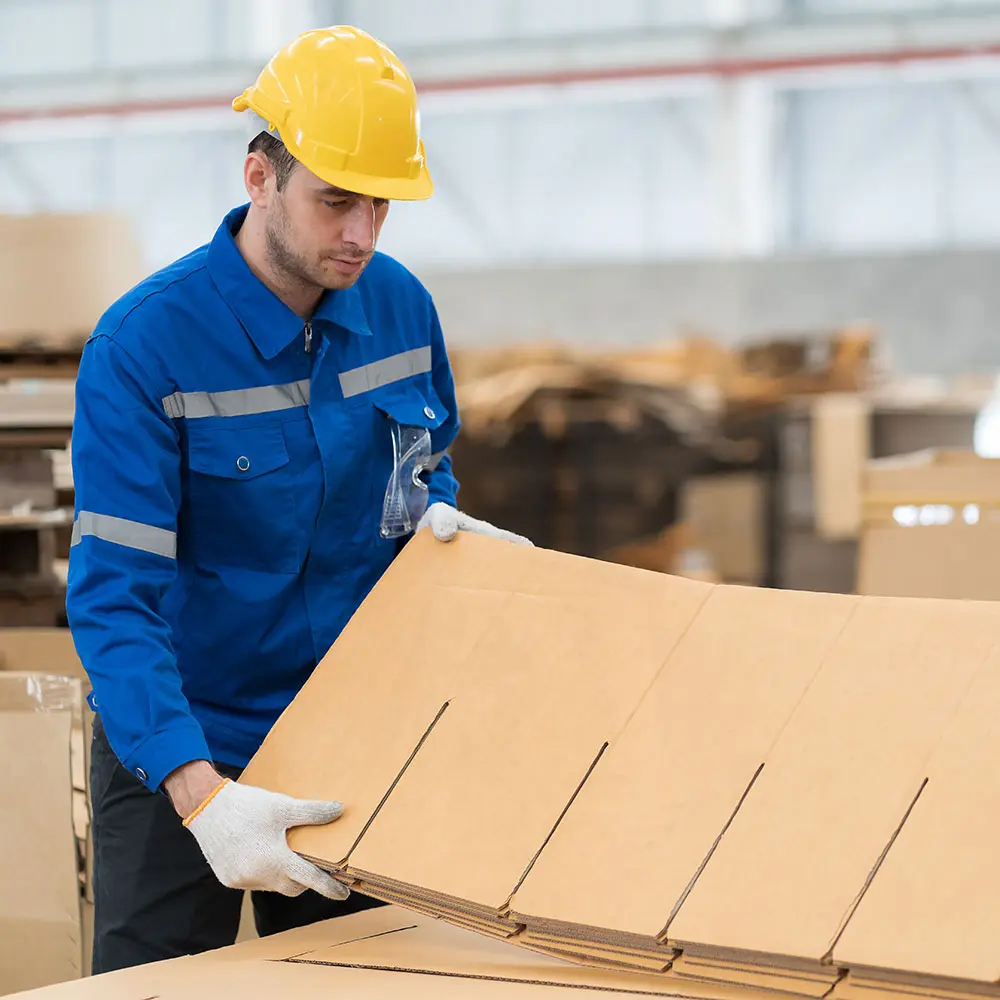
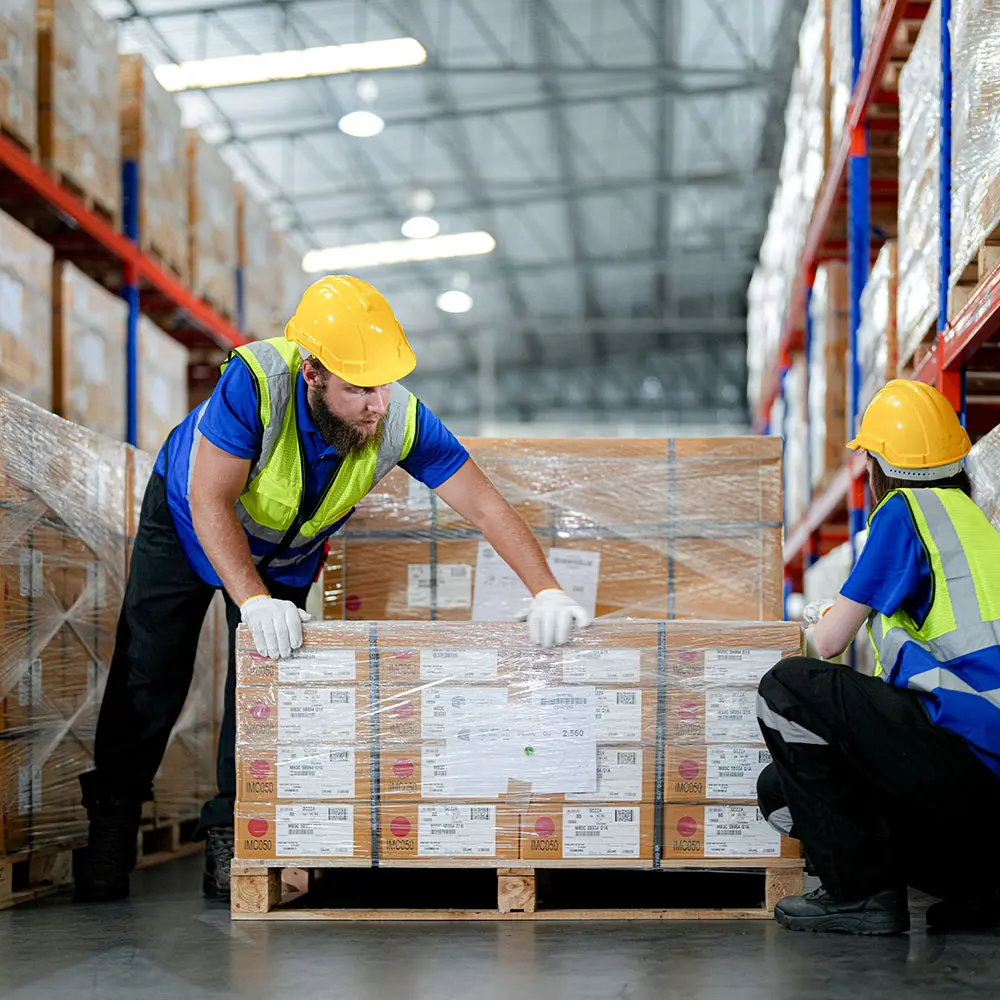
Final Product Testing
Finished products undergo rigorous tests (for thickness, durability, strength, etc.) to meet customer requirements.
Pre-Shipment Inspection
Every order is inspected one last time for damage or defects before shipping.
Tracking & Records
– Documentation and Traceability
We document every step and track materials from start to finish for full transparency
Continuous Improvement
We hold monthly and quarterly KPI meetings to review our quality performance and identify areas for improvement. This commitment to continuous improvement helps us enhance our processes and deliver even better quality products day by day.
Our Packaging Certifications
Beneco Packaging produces products at two locations, both of which operate under Temperature and humidity-controlled environments. This is crucial to maintaining the quality standards of the paperboard products
At Beneco Packaging, quality is at the heart of everything we do. Our Quality Management System is ensured through a dedicated Quality department, internal audits, GFSI (IFS PACsecure) third-party audits, customer audits, and formalized employee training. Our comprehensive QC process guarantees that every product we deliver meets the highest standards of excellence, giving our customers the confidence they deserve.